[ad_1]
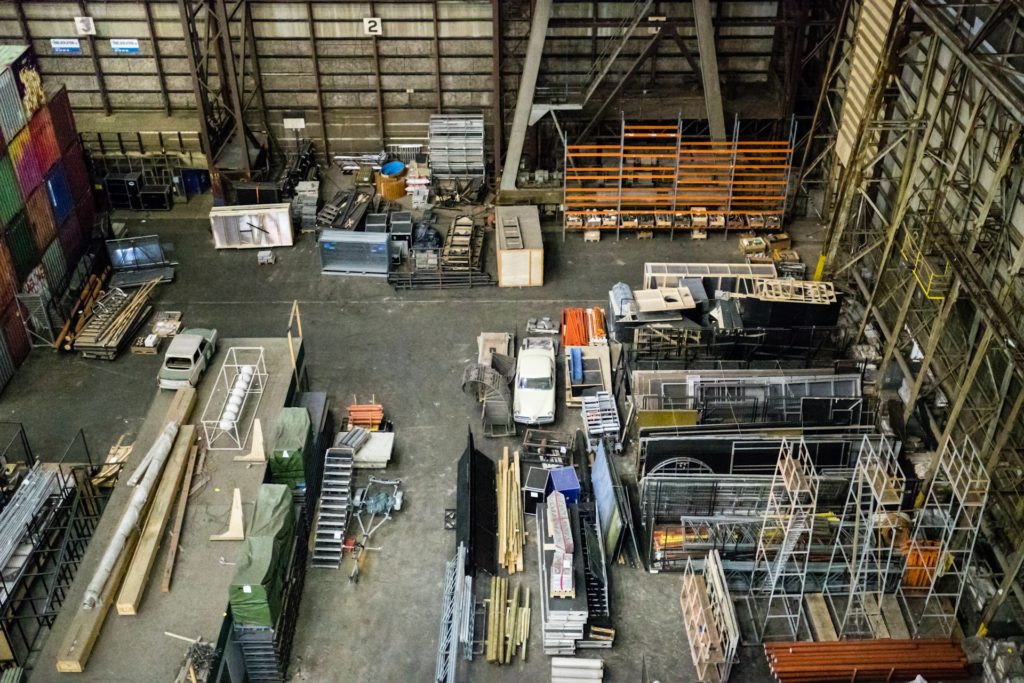
Have you ever struggled to find a standard part that perfectly fits your manufacturing needs? It may be too large or small or need a specific feature. These challenges can lead to inefficiencies, delays, and increased costs. Fortunately, there’s a solution: custom parts. Manufacturers can overcome these obstacles by investing in custom components and unlocking various business benefits.
With that in mind, this article will explore the business benefits of using custom parts in manufacturing, providing insights into how they can enhance efficiency, quality, and overall competitiveness.
1. Enhanced Product Quality
Custom parts are specifically designed to meet the exact needs of the product they’re being used in, ensuring a precise fit and superior functionality. When manufacturers opt for custom parts, they eliminate the risk of using generic components that may not align perfectly with their design or production goals.
By using processes like custom plastics injection molding, manufacturers can produce parts that meet tight tolerances and exact specifications. This leads to higher product quality, fewer defects, and a more consistent result. The ability to tailor each component ensures that the final product is not only functional but also reliable, contributing to an overall higher standard of quality that can help improve brand reputation.
2. Increased Efficiency and Performance
You can optimize custom parts for specific machinery or production processes, which leads to increased efficiency and better overall performance. Moreover, you can significantly reduce production times by designing components to integrate perfectly into the manufacturing workflow, as fewer adjustments or modifications are necessary.
This benefits automated production lines, where precision is crucial for maintaining a smooth, uninterrupted process. By reducing assembly time and minimizing the risk of errors, manufacturers can achieve faster throughput, fewer breakdowns, and higher operational efficiency, all of which contribute to more cost-effective production.
3. Cost-Effectiveness in the Long Term
While custom parts may have a higher upfront cost than standard off-the-shelf components, they are often more cost-effective in the long run. Custom components are designed with durability and performance in mind, so they typically last longer and require less frequent replacement.
In addition, custom parts can help reduce maintenance costs by preventing breakdowns and minimizing production downtime. Over time, these operational cost savings, combined with the increased efficiency they bring to the production process, make custom parts a more economical choice for manufacturers.
4. Competitive Advantage
The ability to produce unique, high-quality products gives manufacturers a competitive edge, especially when using custom components that competitors may need access to. Custom parts allow for more innovation in product design, offering features or improvements that can set a company apart in the marketplace.
By leveraging custom solutions, manufacturers can introduce enhanced performance, better aesthetics, or new functionalities, making them more appealing to consumers. This uniqueness can be precious in industries where differentiation is crucial in attracting customers and building brand loyalty.
5. Better Supply Chain Management
Custom parts can simplify supply chain management by reducing reliance on generic components that may be subject to availability issues or compatibility problems. When a company invests in custom components, it can work closely with suppliers to ensure that parts are delivered on time and in the required quantities.
This reduces the need for large inventories of generic parts that may become obsolete or mismatched with current production needs. Businesses can reduce storage costs, minimize waste, and maintain a more responsive and agile supply chain by optimizing inventory and focusing on just-in-time manufacturing. This close collaboration with suppliers also ensures that any design changes or modifications can be easily accommodated without major disruptions.
6. Flexibility and Adaptability
Custom parts offer flexibility and adaptability that standard components cannot match. As market demands change or new technologies emerge, manufacturers need to be able to adapt quickly without overhauling entire production systems. Custom components allow easy adjustments to part designs, materials, or specifications to meet new requirements.
This flexibility is crucial in fast-paced industries where customer needs and expectations can shift rapidly. By using custom parts, manufacturers can quickly implement design changes, incorporate new features, or adjust for different production volumes, all while maintaining smooth operations.
7. Improved Customer Satisfaction
Products that are made with custom parts often offer better performance, higher reliability, and more precise functionality, all of which contribute to greater customer satisfaction. Customization allows manufacturers to create products that meet the specific needs of their clients, resulting in more tailored solutions.
Custom parts enable companies to address their customers’ requirements more effectively, whether it’s a unique feature, a particular material, or a specialized design. Products that consistently surpass customer expectations foster loyalty and positive word-of-mouth. This increases brand loyalty, positive word-of-mouth, and overall customer retention.
Conclusion
Incorporating custom parts in manufacturing offers many benefits that can significantly enhance a company’s operations. Businesses can improve efficiency, quality, and overall competitiveness by tailoring components to specific needs. While the initial investment may be higher, the long-term returns, such as reduced downtime, increased product performance, and enhanced brand reputation, often outweigh the costs.
[ad_2]