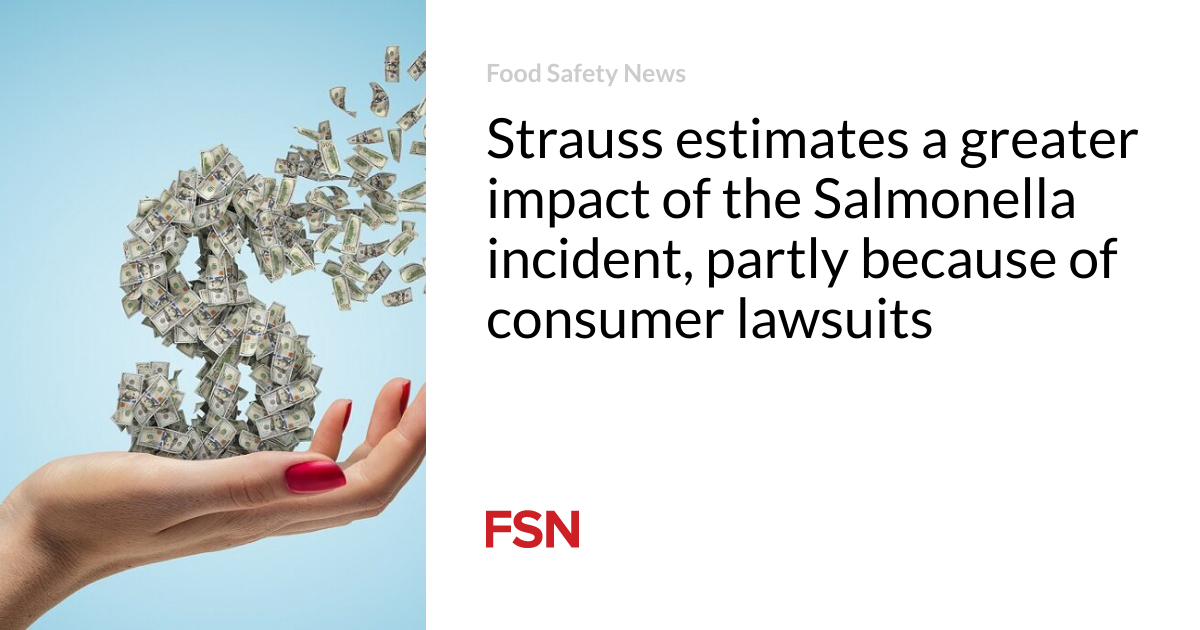
The cost of a recall and plant closure due to Salmonella contamination is to be more than initially predicated, according to Strauss Group.
The company updated the estimated damage to net profit for 2022 due to the recall and shutdown of the plant in Nof Hagalil, Israel to a range of Israeli New Shekel (NIS) 290 to 310 million ($84.8 to $90.7 million).
In May, estimates showed the confectionery recall and closure of the factory would impact net profit for this year by between NIS 170 to 230 million ($49.7 to $67.2 million).
This is based on factors including a decrease in sales, the costs of collecting products from supply chains and points of sale, the estimated scope to destroy inventory, the price of compensating consumers, costs and lost profit due to the gradual resumption of production lines at the plant, and takes into consideration insurance coverage for part of the damage.
Facing consumer claims
Revised figures come from Strauss Group’s financial statements for the third quarter of 2022.
The consequences of the confectionery recall were one of several factors behind a drop in gross and operating profit.
Strauss Israel’s revenue in the quarter was down 10.7 percent, largely the result of a 47 percent drop in sales by the fun and indulgence segment, which was impacted by the recall.
Impact on the company’s results for the first nine months were negative effects of NIS 345 million ($100.7 million) on sales; NIS 341 million ($99.6 million) on operating profit, and NIS 263 million ($76.8 million) on net profit.
Seven motions for class certification are pending against the company as well as another seeking discovery and inspection of documents.
Giora Bardea, the outgoing Strauss Group CEO, said: “Strauss Group delivered growth in most of its businesses, other than the confectionery category in Israel and international dips and spreads. At the same time, coping with inflation and considerable increases in raw material prices, as well as Sabra’s gradual return to the market and the suspension of confectionery operations, have led to margin erosion.”
Return to Market
In August, Strauss received permission to restart production. Approval was suspended in April after an audit by Israeli authorities found Salmonella on a production line and in the liquid chocolate used to make finished products. Elite products were recalled from the United States, Canada, Australia, Brazil, Europe, and the United Kingdom.
Strauss has established a committee to examine the Salmonella incident, discuss courses of action, and make recommendations to the board of directors. Members are Hila Gerstel, Sharon Hannes, and Roni Kobrovsky.
The chocolate production site has restarted manufacturing, and the company is preparing to restock shelves. Some Elite confectionery products will be back in stores in the next few weeks.
The resumption follows investments in product quality and safety. Most production lines are operating and will gradually return to full capacity in three shifts.
The company’s new CEO, Eyal Dror, said products will be returning gradually, based on the pace of production and inventory build-up.
“We are happy and excited to be returning to the shelves. In the past few months, we redefined our work procedures and took steps to ensure especially high standards of food quality and safety based on having learned from the production plants of several world-leading chocolate manufacturers and training conducted by experts. The process of resuming operations on our chocolate production lines included thorough cleaning, upgrading part of the infrastructure, and renewal of the two plants in Nof Hagalil,” Dror said.
Because of adjustments in the chocolate factory, there have been changes to allergen labeling for some products to include eggs, sesame, and nuts as well as milk.
(To sign up for a free subscription to Food Safety News, click here.)